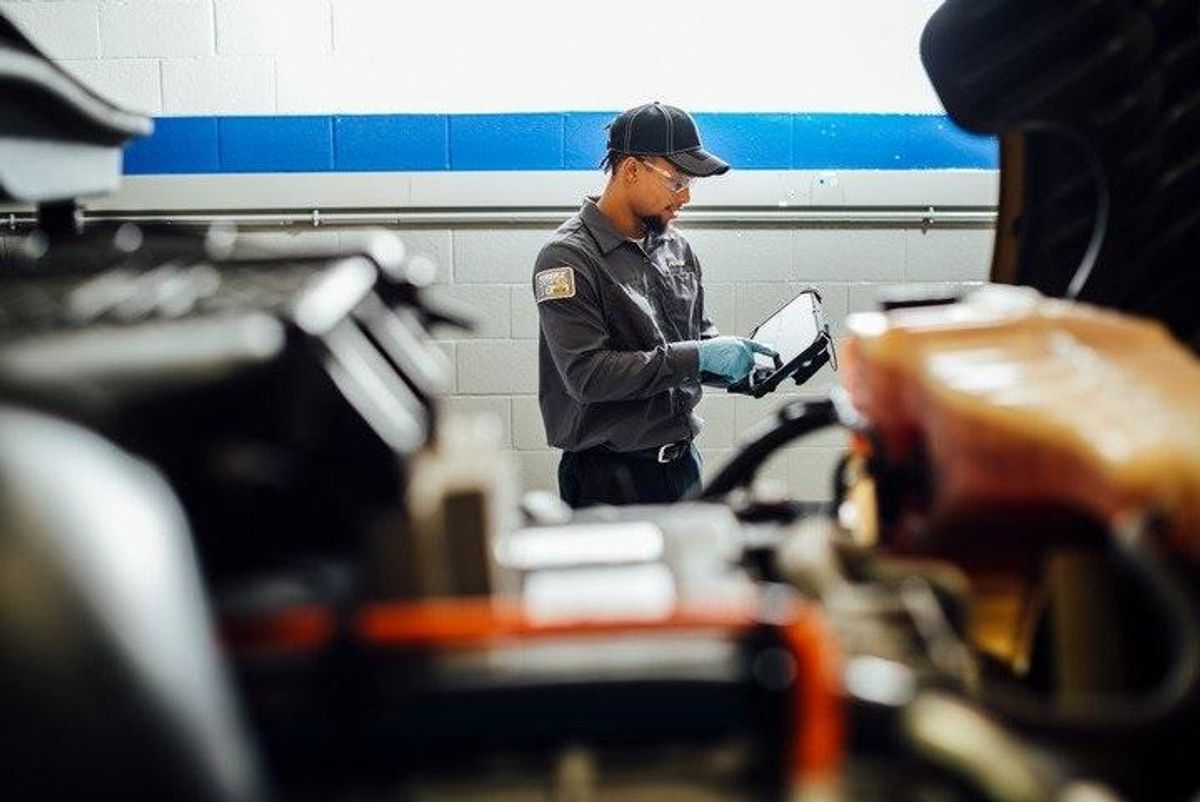
Penske Uses Telematics Data to Improve Uptime and Reduce Driver Frustration
When drawing on telematics information for maintenance, the ultimate goal is to increase vehicle uptime by speeding up, or even preventing, repairs.
“If the vehicle is down for any type of maintenance, that means it is not delivering product,” said Gregg Mangione, executive vice president of maintenance, Penske Truck Leasing. “At their core, fleets want uptime.”
By aggregating and analyzing information coming from the vehicles, Penske can improve its maintenance offerings to speed service, reduce driver frustration and, if possible, get ahead of breakdowns.
Penske recently shared key statistics related to the adoption, selection and utilization of telematics devices in its study 2022 Telematics Use and Trends.
Over-the-Road Repairs
Drawing on data from telematics devices helps technicians understand where the vehicle is, which is important during a roadside repair, and what needs to be serviced.
Information can also help technicians get ahead of problems. "Essentially, we’ve developed some patterns and scenarios where we can see when the vehicle is not operating properly, which helps us improve service,” said Joe Mlachak, vice president at Penske Truck Leasing.
For example, if a check engine light is on, Penske’s coordinators can see fault codes within the vehicle and ensure that service providers are prepared to address them. “Or, if they see that is something we can’t address on the side of the road and they have to bring it to a shop, we can start that process right away,” Mlachak said.
When a driver needs an over-the-road repair, telematics data helps direct maintenance technicians to the right location. “That cuts down time spent trying to find the vehicle,” Mlachak said.
Proactive Diagnostics
Penske goes beyond looking at single instances of critical fault codes. “We look at the patterns of codes that could lead to a particular breakdown, and we develop scenarios off of those patterns,” Mlachak noted, adding that sometimes a driver may not even detect that anything is wrong with the vehicle.
Still, Penske knows there is an issue that will lead to a breakdown. “We alert the shops first, and in some time sensitive cases we will attempt to alert the customer directly," Mlachak added.
Penske has started using deep learning, an advanced AI method, to predict breakdowns based on miles, or time, in order to get ahead of repairs. As part of the process, Penske accounts for the vehicle's duty cycle. “If it is running on the highway at 70 miles per hour, it will react differently to problems than one operating in the city,” Mlachak said.
Temperature also factors into the decision-making process. “What our scenarios look like in the summer is different than the winter. We’re also able to tweak our scenarios regionally to determine what applies to those vehicles,” Mlachak said.
With proactive diagnostics, fleets can reduce road calls, which can help limit driver frustration, improve safety and cut costs. "Road calls are expensive. The cost of most engine related road calls may be upwards of $1,000 for a fleet owner. Towing costs can further increase that figure," Mlachak said.
Length of Repairs
Drivers’ hours-of-service requirements are a significant issue, so fleets want to know how long a driver will need to wait for a repair. "We’re able to take scenarios using fault codes, and match them up to other technology that we’ve developed within the company, to estimate the scope of the repair and the time it will take to get the vehicle back on the road,” Mlachak said.
Maybe even more importantly, data can help minimize driver frustration.
“I’ve been in a shop where a driver was able to limp the vehicle in with a check engine light but was very frustrated. He was empty, and all he was looking to do was get home,” Mlachak said, adding that it takes more time if technicians are starting their diagnosis from scratch. "If we can potentially address that driver’s concern before it gets to that stage and supply that technician with diagnostic information, we collapse the cycle time and get the driver home faster.”
Improving driver and technician satisfaction is critical as both fill vital roles within the supply chain.
To learn more about Penske and its maintenance services, please dial 844-376-4099.
By “Move Ahead” Staff